Batteries for electric buses (3/5)
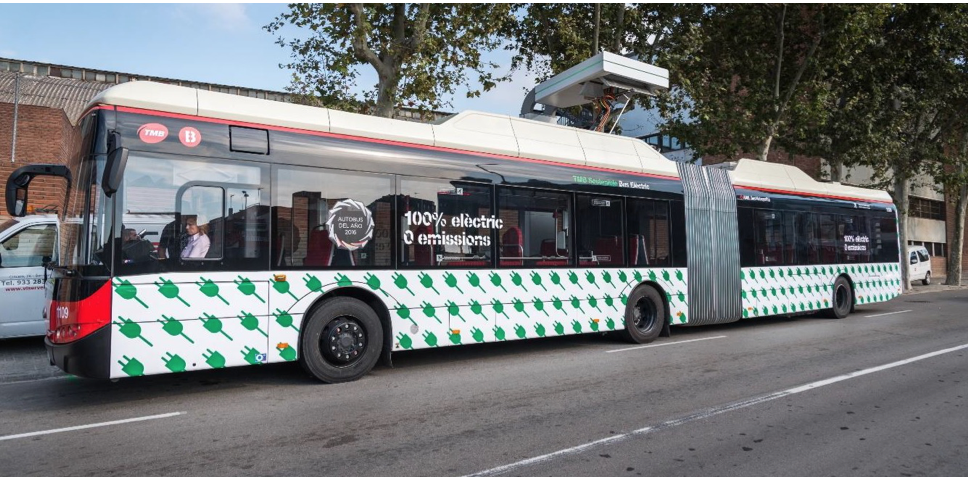
In the last article of the Battery University, we focused on the selection of the optimal traction battery technology for the partial trolleybus. While the requirements for a partial trolleybus are very similar for most of the projects, it is different for electric buses. The requirements for the use of electric buses vary greatly from project to project, whether we are considering an intercity vehicle, a suburban vehicle or the most frequently used electric bus for purely urban public transport.
Unlike partial trolleybuses, the operator must also deal with the charging infrastructure when purchasing vehicles. Thus, the electrification of bus transport in cities is a comprehensive solution for suitable vehicle technology, their traction batteries and a suitable charging strategy.
Mileage, that's what it is all about
Already at the beginning of the article, we named various types of electric bus operation, which mostly copy classic buses. The most common talk is about electric bus transport in cities, which is also the most supported in terms of various subsidies. This fact is understandable given the emission-free transport commitments that various world capitals publish.
Also, the numbers of registrations of electric buses over 3.5 tons show that the market of electric buses is starting to grow. According to data from the European Automobile Manufacturers Association from April 2020, the year-on-year increase in so-called ECV (electrically-chargeable vehicles) was 170.5%. In absolute numbers, this is an increase in registrations from 594 in 2018 to 1607 in 2019. Nevertheless, the share of newly registered buses over 3.5 tonnes with diesel was 85%.
For electric buses – whether it is urban, suburban or long-distance traffic – it is important how many kilometers it is able to drive during the day. Because there is still not a sufficiently universal battery technology that allows similar journeys on a single charge as in diesel buses and at the same time with a similar charge time as in refueling, we must choose the appropriate traction battery technology for a particular operation. So let’s take a closer look at what we need to consider when choosing the right battery for electric buses.
Electric buses in the city
For the electrification of city bus transport, it is very important to evaluate the possibilities of building a charging infrastructure. While electric cars already have only a few charging standards, differing mainly according to the continent where they are used, charging standards are still coming for electric buses. As well as the choice of charging method, the choice of charging frequency is important. In the operation of an electric bus in city transport, it is possible to work with the frequency of charging according to the possibilities of building infrastructure.
Charging at stops
Imagine the future, the electric bus stops at a stop and during the first seconds automatically connects to the charger and charges enough energy to drive to the next stop. The whole process takes only a few tens of seconds and the vehicle continues to the next stop. What sounds like science fiction, already exists. Passengers in Geneva have been experiencing this vision for the future since 2013. One of the key elements is the TOSA 600 kW charging system, the other is the traction battery of the electric bus. Let’s take a closer look.
Logically, if a charge of 600 kW for 20 seconds is sufficient to reach the next stop, the traction battery can be very small. Let’s say that the total consumption of an electric bus is 1.5 kWh / km. Charging 600 kW for 20 seconds will give the batteries 3.33 kWh (actually a little less because charging losses need to be included), which would be enough to cover 2.86 km. The number of cycles for each day of operation will also be very large and the capacity of the battery must be chosen so that the battery is able to withstand high charging and discharging performance while achieving the expected life of many years.
If we take a closer look at the life of the traction battery, resp. traction battery technology, we are interested in the cyclic one. Each battery technology has its own cyclic life, which depends on the depth of discharge of the battery (amount of energy in % taken after each charge and the average temperature of the cells). Sometimes it also refers to the C-Rate (battery power / capacity ratio), but the C-Rate affects the available capacity (the higher the power, the less capacity the battery can be discharged or charged) and the temperature (higher C-Rate = higher thermal battery loss). Cyclic life is most often characterized by either a curve (example Graph 1) or a table (Example Table 1)
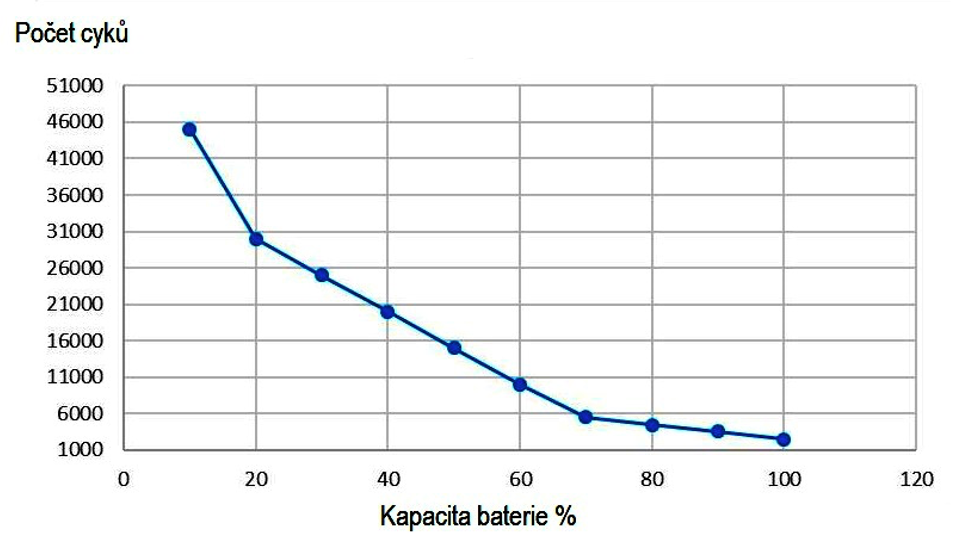
Cell average temperature (C°) | |
Depth of Discharge DOD (%) | |
Cycle life (number of cycles until 80% of the original capacity is reached) |
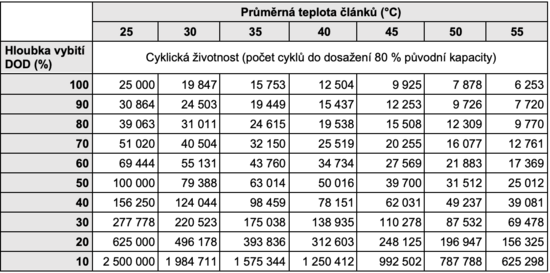
So how do you choose the right battery to charge at bus stops? As we have said, the battery should be as small as possible in terms of weight, size and capacity, at the same time it should be able to charge with high power (eg according to Geneva 600 kW) and last in operation for several years. For myself, I would prefer the same battery life as an electric bus, which is possible, but in the initial investment more expensive approach. It is also possible to plan one replacement of the traction battery during the lifetime of the vehicle or to agree with the vehicle manufacturer on a battery warranty for the lifetime of the vehicle – the associated costs are reflected in the price, but eliminates the uncertainty associated with the timing of replacement. If we plan a lifespan of 12 years, it is therefore possible to choose a battery for 6 years and replace it after 6 years, or choose one that will last for 12 years. For a type of operation such as Geneva, technologies other than LTO are not possible.
The reasons are clear. The LTO (lithium titanate) we mentioned in Table 1 handles short-term 12C charging. If we take the traditional power of fast bus chargers 450 kW and divide by 12, we get a capacity of 37.5 kWh. Thus, if we consumed 3.75 kWh before each charge and recharged it when charging at the bus stop, the DOD discharge depth in% would be only 10 % and the battery would do 2,500,000 cycles before reaching 80 % of the original capacity (assuming that we would keep the average cell temperature at 25 ° C.
So consider a service life of 12 years with 360 days of operation per year. That’s a total of 12 × 360 cycles = 4320 days of operation. If we divide the number of LTO battery cycles by the number of days in 12-year operation, we get 578 cycles per day.
The number of charged stops could therefore be up to 578 each day of operation, so that the battery has 80 % of its original capacity after 12 years, ie 30 kWh.
Comparison of two different existing battery systems
TITAN RAPID is an LTO battery system designed for ultra-fast charging, has a capacity of 42 kWh and is divided into two battery boxes, each measuring 1380 × 713 × 360 mm with a total weight of 950 kg.
AKM POC is an NMC battery system with a capacity of 176 kWh, it is divided into five battery boxes, each measuring 1546 × 750 × 216 mm with a total weight of 1665 kg.
At purchase price, both batteries will be almost equal (slightly in favor of LTO), but the weight is clearly better with LTO, as well as the volume needed to install the battery in the vehicle. For NMC batteries (Lithium nickel magnesium cobalt oxide) a volume of 1.25 m3 is required, for LTO TITAN rapid batteries a volume of 0.7 m3 is required.
Evaluation of operation with frequent charging
The more often an electric bus is charged, the more it can use small and powerful batteries, for which LTO chemistry is ideal. This approach seems to be optimal for urban traffic, but it encounters the need to build a powerful and expensive charging infrastructure.
However, if we choose the path of continuous charging with a sufficiently high power, such as at final stops, it is possible to take advantage of the LTO mentioned in comparison with LTO and NMC and use a relatively small but powerful battery. Unlike NMC technology, it allows continuous operation 24/7, as it is able to fully charge from 0 to 100% in a few minutes, while with NMC and other high energy batteries it would take several hours. An example is the city of Ostrava, which has two electric buses in operation with this LTO traction battery, able to be charged for another hour in 5 minutes.
But what batteries will we look for when it is not possible to build such infrastructure in the city?
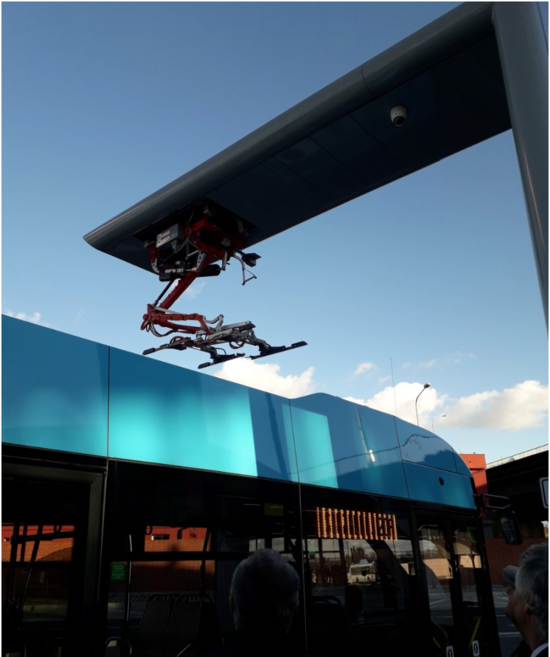
Electric buses with night charging
Electric buses designed for overnight charging need sufficient capacity of the traction battery to travel the all-day route, which is charged overnight at the depot. Thus, one property is very important for traction batteries, and that is specific energy. The specific energy expresses the ratio of capacity and weight of the traction battery, ie how much Wh can fit in 1 kg of battery weight. Graph 2 shows the specific energy of the most commonly used types of battery cells. These are therefore separate cells without the included modularization, battery boxes, cooling, electronics, etc.
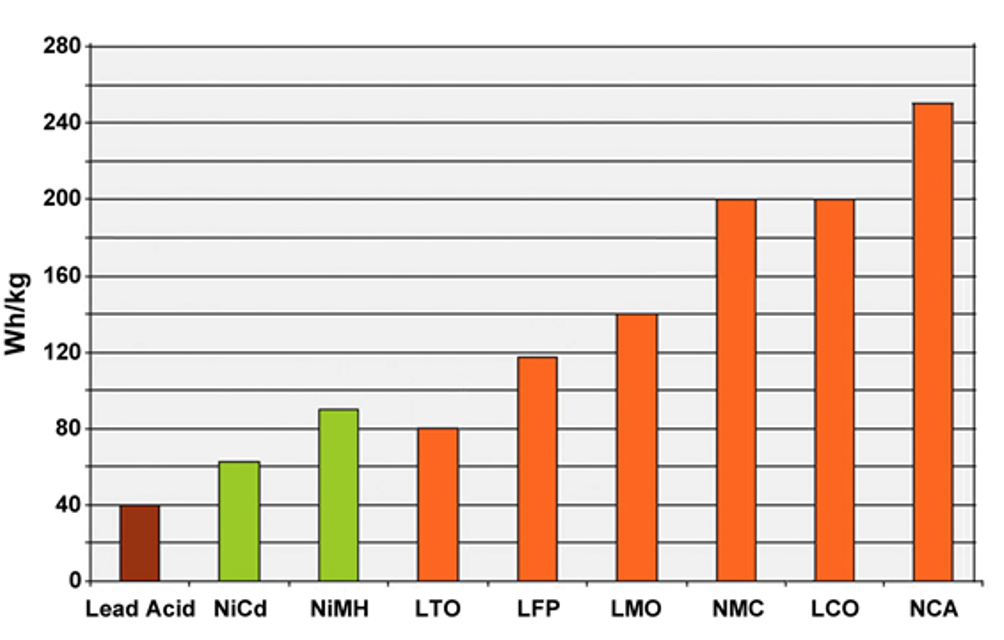
All-day batteries have such a high capacity that the power they give to drive the vehicle generally does not exceed C-rate 1C, i.e. that the power of the motor (s) is less than or equal to the capacity of the traction battery. So the amount of energy is absolutely crucial, and if we set the limit weight of the traction battery, we choose the technology that has the largest capacity per unit weight.
Chart 2 shows that it is NCA technology. NCA or Lithium Nickel Cobalt Aluminum oxide has the highest density of commonly used types of lithium batteries today. Manufacturers achieve specific energies between 250 – 280 Wh / kg and in the laboratory are already approaching 300 Wh / kg.
The disadvantage of NCA cells is that they allow relatively few charging cycles compared to, for example, NMCs. Nevertheless, NCA has become a key technology in the automotive industry for the production of electric cars. And here is the stumbling block of the use of this technology for electric buses. The largest manufacturer of NCA cells is the company Panasonic, which has its capacities booked long in advance for several major manufacturers of electric cars, especially for Tesla manufacturers. The availability of these articles for other potential integrators is therefore small, rather zero.
This is the next in line, and that is NMC. LCO or Lithium Cobalt Oxide is not a suitable technology for electric buses because, unlike NMC (Lithium Nickel Magnesium Cobalt Oxide), it is less safe, has fewer cycles and is not suitable for short-term performance above 1C. In the case of so-called high energy electric buses, ie those with a high-capacity battery, we usually encounter NMC batteries.
We also have several similar operations. An example is the city of Třinec, where since 2017 ARRIVA has been operating a fleet of Škoda Perun HE electric buses with Li-Pol (lithium-polymer) traction batteries with a capacity of 222 kWh. According to available information, these buses can travel 150 – 200 km on a single charge, followed by overnight charging for about 6 hours.
Here it is necessary to add the difference between Li-ion and Li-Pol batteries. Simply put, they are both very similar, with Li-ion the electrolyte is liquid, while Li-Pol is not and most often occurs in the form of a gel. However, the positive electrodes in both are the same, most often NMC, LFP or LCO. However, they are more expensive to manufacture compared to Li-ion batteries.
Another example is the town of Hranice, where the carrier 3CSAD operates urban transport with its electric buses. SOR electric buses run between 50 and 150 km per day. Unlike Třinec electric buses, the vehicles here are equipped with LFP batteries (lithium iron phosphate) with a capacity of 172 kWh.
Charging infrastructure for night charging
Night charging is usually solved in the same way as for electric cars, ie using charging standards such as CCS2 COMBO. This has the advantage that this standard is mass-tested.
How to choose a suitable battery for night charging
Unlike the example with frequent recharging, where LTO technology clearly dominates, the choice of a suitable battery for night charging depends on the specifics of a particular operation. For smaller cities, where there are short routes and the frequency of lines is not so high, so the total daily run will be shorter, say about 100 km, LFP batteries will probably be more suitable. Although the specific energy parameter is significantly worse compared to NMC, it is cheaper and reaches more cycles. It also manages a higher C-Rate compared to NMC in the short term.
On the contrary, where daily runs on a single charge are longer, NMC technology will be suitable over 100 km, because it is possible to get more than 1.5 times as much energy in kWh for the same weight as LFP batteries.
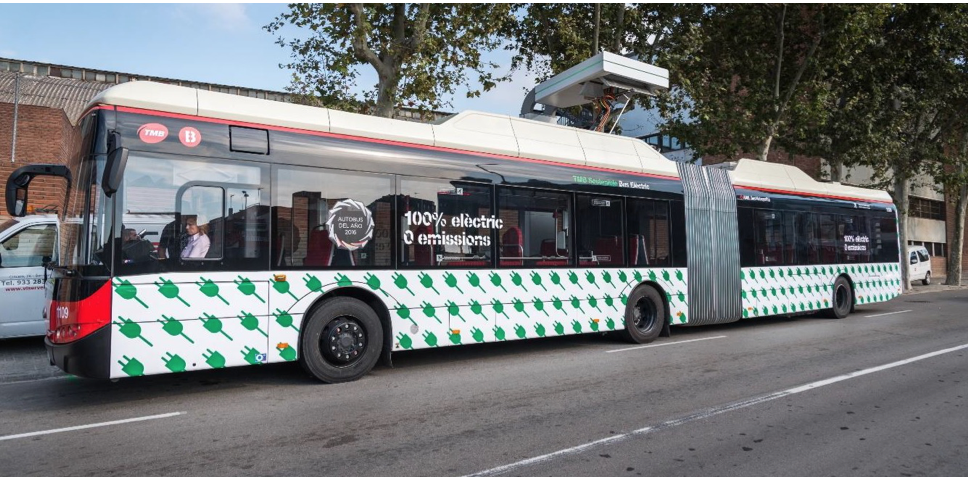
Summary
From the point of view of building the infrastructure for charging electric buses in operation, a more suitable variant of vehicles with night charging seems to be suitable. However, this is due to the growing consumption of electric buses due to higher demands on non-traction consumption, ie energy for systems that are not directly connected to the drive, such as air conditioning, heating, information and check-in systems, etc. The result is limited range per charge, which may be sufficient for daily traffic in small towns, but not for large cities with bus service on the line even 20 hours a day.
The most suitable is the combination of both approaches together, ie occasional charging during operation in combination with night charging.
The choice of traction battery technology thus depends very much on the requirements for vehicle operation (length between charging, weight, service life, etc.) and it is not possible to say which battery technology is most suitable for electric buses.
An example of the final comparison is the exit of the ZeEUS project from Barcelona, where a comparison of two different operating strategies took place – continuous charging with the Schunk bus-up standard and night charging after all-day operation. On both types, the vehicles had a daily range of about 180 km and the end of the project is that the technology of continuous charging is more suitable for urban traffic in a large city such as Barcelona.
František Šťastný