Battery life
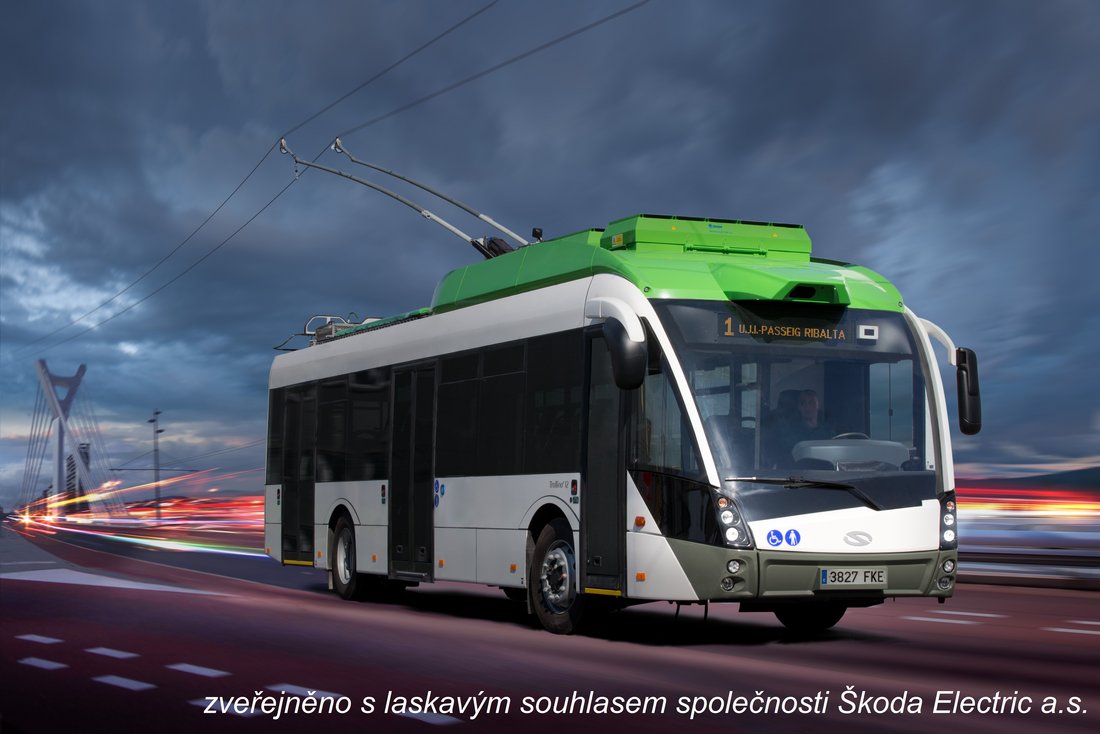
Batteries and accumulators are an integral part of our lives today. Without these electrochemical energy sources, we cannot imagine life today. They are all around us, in every mobile phone, TV remote and in every car. With the advancement of electromobility, however, the word battery or accumulator is increasingly used interchangeably. Here we will show you how to understand batteries and their efficient use in electromobility, whether they are passenger or freight electric vehicles or electric buses.
Batteries and Accumulators
The difference between a battery and an accumulator must be explained first.
From an electrochemical source of energy, a battery is a collection of one or more primary cells, those that cannot be recharged.
An accumulator is an electrochemical source that consists of one or more secondary cells, which can be recharged after discharge.
Thus, the primary driver of a television remote control are primary cells, mobile phone batteries, car starter batteries and electric vehicle batteries are secondary cells and should correctly be labelled as accumulators. Today, however, the terms “battery” and “accumulator” are used interchangeably, and the term “battery” is commonly used for assembling rechargeable cells, such as traction batteries – that is, batteries which serve as a power source to power an electric vehicle.
Battery life – an essential element in electromobility
It is electromobility that raises a lot of questions about how to actually utilise batteries in order to attain their longest life. The European Environment Agency (2019) site reports that in 2018 the total proportion of electric vehicles, i.e. plug-in hybrids (electric cars charged from the outside while equipped with a combustion engine) and pure electric powered vehicles, amounted to 2% of the total 257 million vehicles. The experience of electric vehicles amongst the general public is therefore not great, and even amongst professionals there are many myths about battery-powered vehicles. The most pressing issue is the battery life of the electric vehicle. Let’s explain what will affect the electric vehicle’s traction battery life most, and it doesn’t matter if it’s an electric car or bus.
Electrochemical source selection
The first element that affects the life of the traction battery is the choice of the electrochemical source. Today, almost invariably, lithium-based accumulators are used without exception in electrical mobility. This was not always the case.
The second method was by using alkaline batteries Ni-Cd or Ni-MH. These chemical compositions no longer suffered from degradation without regular charging, as with lead-acid batteries. However, the development of electromobility fully enabled the arrival of lithium-based batteries. Even in the field of lithium accumulators themselves, there are many subgroups according to the elements used in the electrodes, and these determine the final characteristics of the traction battery itself.
The first example of life expectancy
The first electric vehicles used traditional lead-acid batteries, but these are not ideal as they degrade very quickly if they are not regularly charged to full capacity. A typical example of such is the electric car, the ŠKODA ELTRA 151L and 151 Pick-UP from the early 1990s.
Number of charging cycles
The life expectancy of the traction battery is defined by two indicators.
The first is the calendar life, which is the theoretical amount of time a battery is maintained at full charge before it reaches 80% of its original capacity.
The second indicator, and much more important for the requirements of electromobility, is the cyclic life. Cyclical life refers to how many cycles of charge and discharge a given battery will achieve if repeatedly charged and discharged. The number of such cycles then depends on the depth of discharge (DOD) and the average temperature of the battery cells over it’s lifetime. An example of the definition of the cyclic life of a lithium battery for the chemical variant of a lithium titanate battery (LTO) is shown in the table.
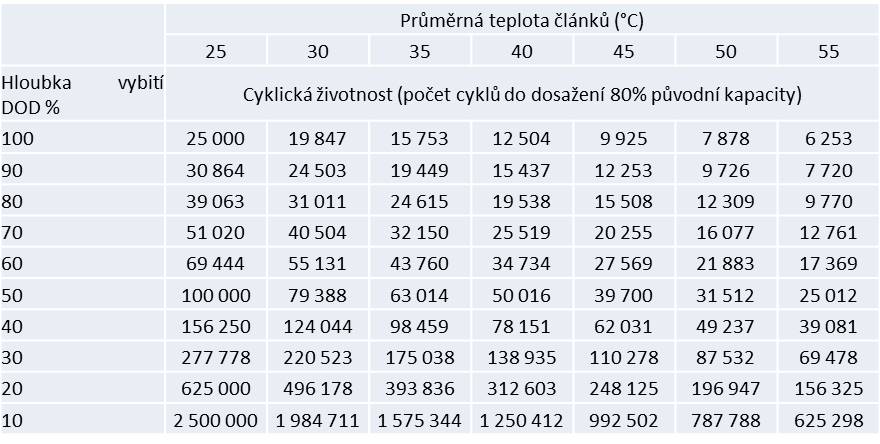
Other types of lithium batteries have different cyclic life characteristics.
The above mentioned lithium-titanate batteries (LTO) have the most cycles, in our case 39,000, with a regular discharge of 80% battery power (80% DOD). The LTO accumulators are also suitable for applications where high performance is needed, that is, very fast charging and discharging, but have a lower energy density (Wh/kg) than other types of lithium accumulators, therefore they are not suitable for applications with a very long range per charge.
Conversely, lithium magnesium cobalt (NMC) batteries have one of the highest energy densities in Wh/kg and are therefore suitable for applications where high range per charge is required.
In contrast, cyclical lifespans. Some manufacturers report up to 6,000 cycles using 80% of battery power (80% DOD) on a regular basis. To achieve a lifespan similar to that of LTO traction batteries, the NMC traction battery capacity needs to be adequately increased and only part of it used regularly.
A disadvantage of all current lithium batteries with high energy density is their inability to charge quickly. Some types are capable of charging up to 2C, which means that the charging power (kW) can be twice the battery capacity in KWh.
In contrast, the most powerful LTO batteries are capable of achieving 8C charging power. Converted to charge time, this means that the LTO battery will charge from 0 to 100% in 7.5 minutes, while the NMC battery will charge in 30 minutes.
However, the charging time issue must include one more indicator, namely cell temperature. When charged with high power, cell temperature increases rapidly due to heat losses caused by an increase in cell internal resistance at higher currents or charging performance, respectively. From the point of view of the whole traction battery system, this means that fast charging systems (2C for NMC and 8C for LTO batteries) must have an adequately sized cooling system.
Nowadays, we often find that fast charging of traction batteries is detrimental. A survey by Geotab (see graph in the figure), which focused on several areas of traction battery evaluation, highlighted the fact that traction batteries suffer from a faster overall drop in the capacity of the traction accumulator in personal electric vehicle use.
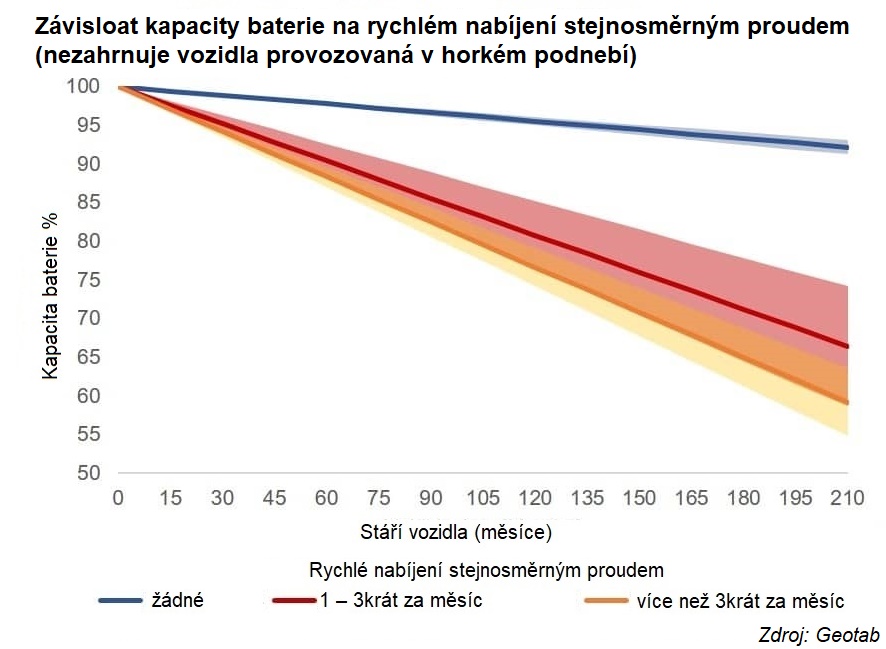
However, this chart does not take into account the design of traction batteries, since both electric vehicles that have passive cooling of the traction battery and those that have advanced liquid cooling were included in the survey. Such batteries will vary greatly in average cell temperature. Passive-cooled batteries will have a significantly higher cell temperature over their lifetime, and thus their overall capacity drop will be significantly faster compared to active liquid-cooled traction batteries.
The second exmple of life expectancy
The cyclical lifetime of LTO batteries is predominantly used in partial trolleybuses, i.e. trolleybuses with battery energy storage for operation outside the trolley. Such a vehicle extends the line many times a day beyond the reach of the overhead contact line and is able to travel 10 to 15 km on a small traction battery, depending on the size of the vehicle. Users can ideally extend the line without having to build the overhead lines. Despite the fact that there are more than 10 daily journeys beyond traction line range in real applications, traction batteries have the ambition to realistically achieve vehicle life.
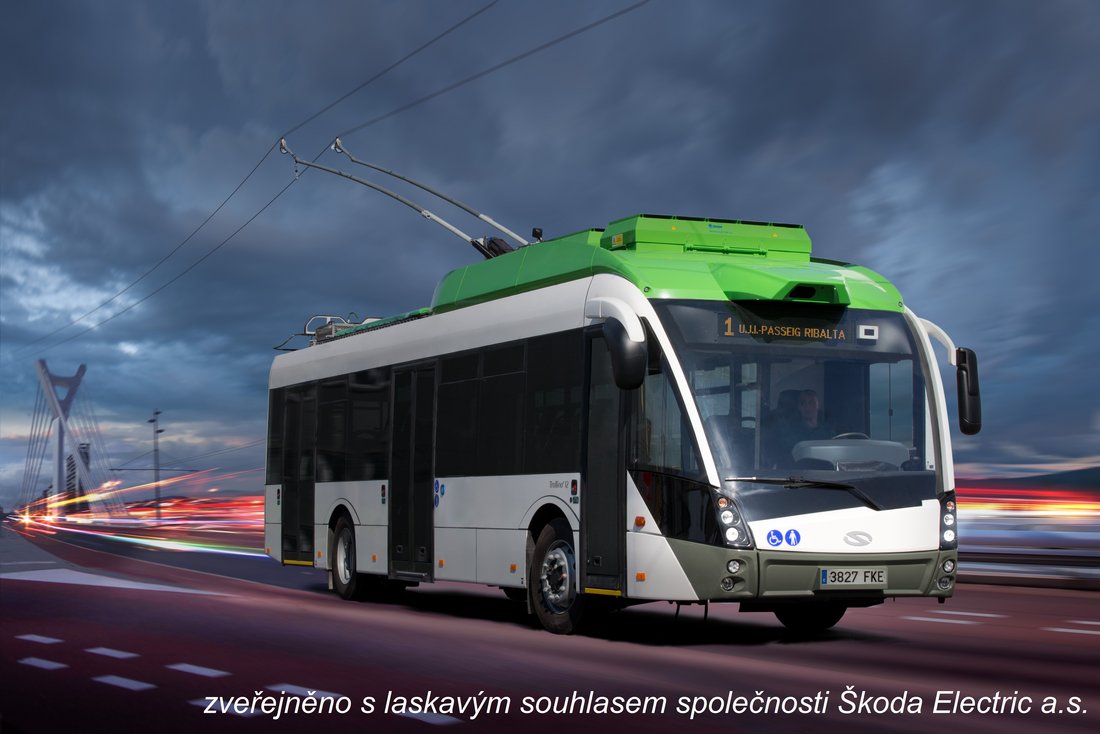
The third example of life expectancy
Continuous charging of electric buses is an example of the use of fast charging LTO batteries. In the Czech Republic, the application of this technology in the electric bus can be found in the city of Ostrava, which operates two electric buses with traction LTO batteries on the Ostrava-Svinov – Klimkovice line.
The whole line is designed so that at the final station Ostrava-Svinov there is a fast charging station with an output exceeding 400 kW, which in five minutes charges the traction battery for another hour of driving.
The vehicle needs a relatively small traction battery with a capacity of about 80 kWh, because the vehicle for the entire circuit uses about 50% of its installed capacity. Despite the fact that the battery will perform 12 to 15 charge-discharge cycles per day, the planned lifetime of the traction battery is more than ten years.
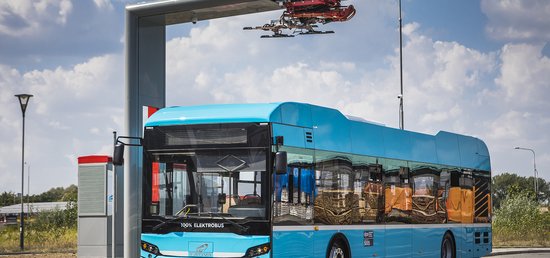
How to extend battery life
The overall battery life can be extended in a few steps.
The first is to choose the right technology for a specific application. When considering the electric bus, the first question is whether it is purely to be utilised for urban traffic or whether it is a vehicle designed for longer journeys.
The next step is to determine the strategy for developing the charging infrastructure with respect to the expected charging frequency. A different lifespan will have a battery that recharges regularly in service, in extreme cases at each stop, and a different lifespan will have a battery that recharges at night at the depot after a day’s operation. For frequent charging during service, LTO technology that is capable of accommodating high amounts of energy in a short period of time and whose high cyclical life will enable traction battery life to be achieved at the same level as the vehicle life expectancy can be chosen. On the other hand, another traction battery is suitable for longer range and night recharging.
The last step is to select the size of the traction battery, i.e. the amount of energy in kWh. As the available accumulator capacity decreases over the course of its life, the traction battery must be designed to provide the required energy even at the end of its life. Simply put, the electric vehicle will continue to travel the desired route at the end of its life. Here we do not necessarily follow the generally accepted view that the end of battery life is reaching 80% of its original capacity. For lithium batteries, this limit can be pushed down, say to 60%, because the total capacity drop for lithium batteries is roughly linear.
The fourth example of life expectancy
Our real use examples of traction batteries show the status of traction batteries post several years of operation. The oldest partial trolleybuses with LTO batteries manufactured by Škoda Electric have been running since 2014. According to current battery status measurements from 2019, the traction battery capacity is reduced to 2%.
For Ekova, manufacturers of electric fast-charging electric buses operating in Ostrava, the current capacity drop is less than one percent compared to the original capacity at the beginning of life expectancy after about 80,000 kilometres. Due to the fact that both applications use about 50% of installed capacity, the traction batteries on these vehicles have a long service life. In these cases, end-of-life can be planned somewhere at 70% of the residual capacity of the traction battery.
In conclusion
Battery life is therefore a matter of choosing the right technology for a particular application, not just the type of accumulator, but the traction battery as a whole, including its size and correct cooling technology. The service life itself can then be influenced by the user, related to proper charging. In the case of lithium accumulators and after use in vehicles as part of traction batteries, these can be used in stationary repositories where they can be used for many more years.
František Šťastný
Photos and pictures © nano power a.s., unless otherwise stated