Batteries for partial trolleybuses (2/5)
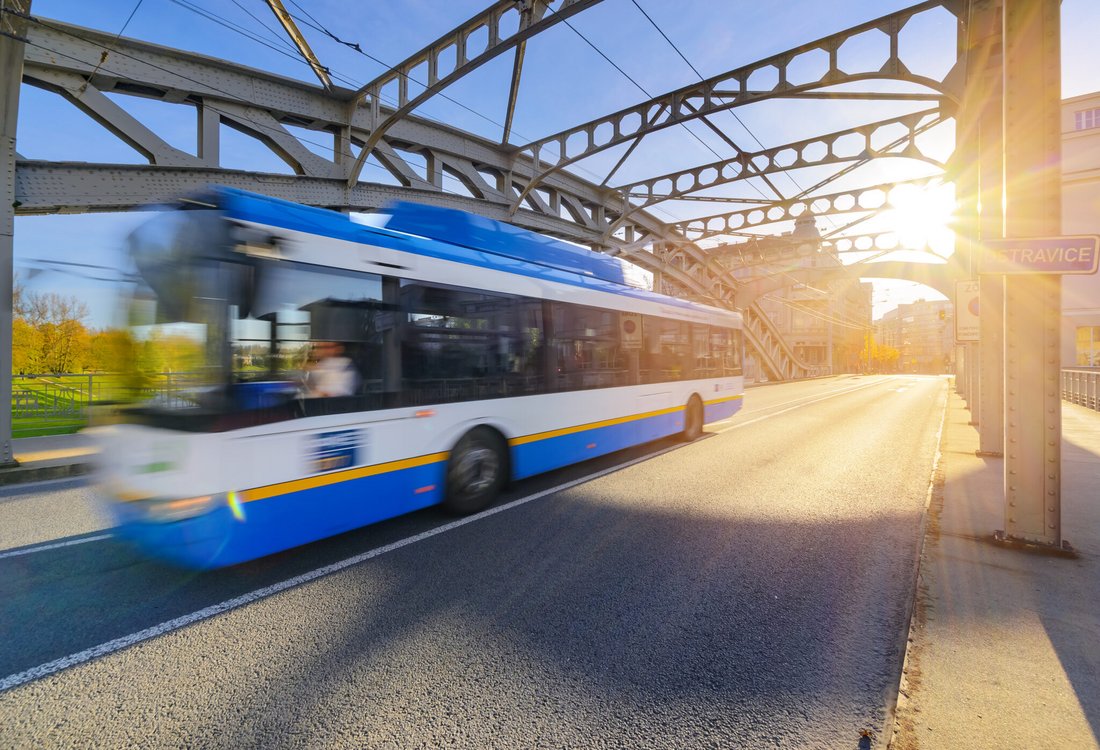
The first article from our Battery University introduced the reader to problems of batteries used to power vehicles. Our second article aims to provide users and investors in trolleybus transport with a comprehensive view of the choice of alternative trolleybus drive, especially battery drive for partial trolleybus.
History of trolleybus
Partial trolleybus is a relatively new concept that emerged with the advent of electromobility and the use of traction batteries in public transport vehicles. However, the trolleybus itself is a vehicle known for more than a hundred years. The first trolleybus saw the light of day in 1882. It was called Elektromont and its inventor was Werner von Siemens. The vehicle, which looks like a horse-drawn carriage, drove in trial for 6 weeks in Berlin.
Here we can see an interesting parallel: While the first electric car appeared in 1835 and in 1899 the first electric vehicle broke the 100km / h limit, the first trolleybus was put into operation in 1882 and the first internal combustion car was patented in 1886. Electromobility thus, already at the beginning of the transport revolution – the replacement of horse-powered by an engine – had a considerable advantage. However, it had to wait much longer for its development than the internal combustion engine. Unlike electric cars, however, the trolleybus kept its place in the sun all the time and developed as a unique means of public transport. The oil crisis in the 20th century also contributed to its development.
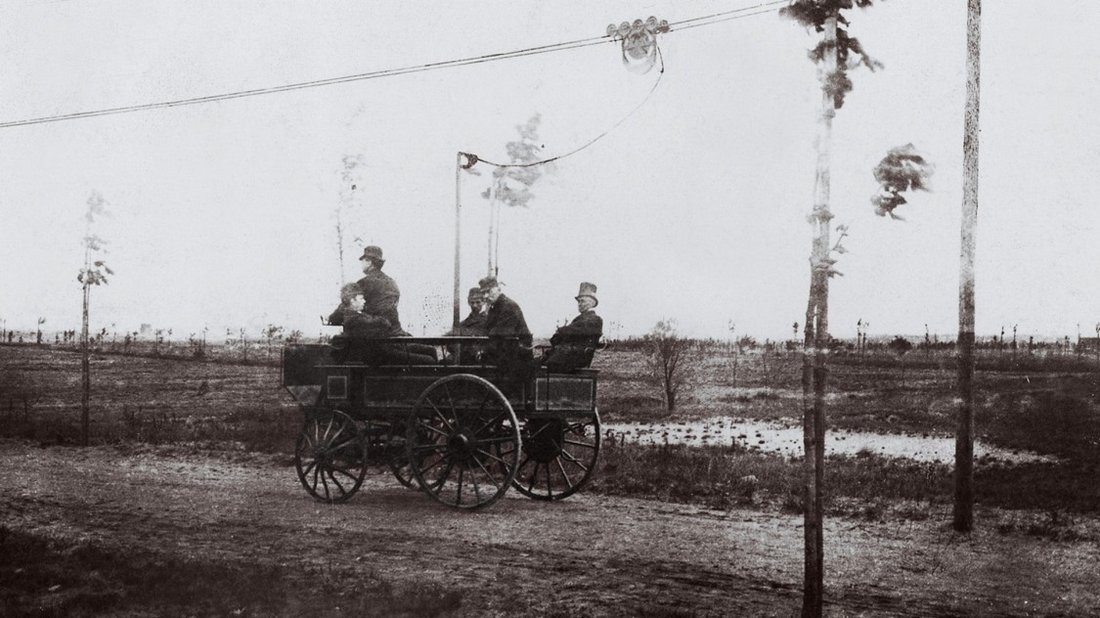
Trolleybus without trolleys - Diesel vs. battery
Before we take a closer look at the individual technologies of the traction batteries of the partial trolleybus, let’s look at where the partial trolleybus actually came from. In order to reduce their operational weakness in the form of dependence on the traction line in a very variable street traffic environment, trolleybuses with additional drive or hybrid trolleybuses (trolleybuses with auxiliary drive or partial trolleybuses) were created. The hybrid drive allows driving outside the trolleybus traction line. This drive can be battery or motor.
Here it is necessary to distinguish whether it is an auxiliary drive, which is not intended for full-fledged driving, or a full-fledged drive, thanks to which the trolleybus is out of reach of the traction line as a full-fledged vehicle. While the auxiliary drive is usually used for occasional short-term use without trolleys, such as driving in a depot or for short journeys on a line outside the trolley, a full-fledged drive must allow the trolleybus to ride with the same comfort as when driving under trolleys and longer distances.
As for a motor drive, a diesel unit is used, which produces electricity for the traction engines of the vehicle, usually as an auxiliary drive. However, this solution encounters a serious problem, and that is the characteristics of the operation. The diesel unit starts when the trolleybus leaves the traction line, the vehicle travels a few kilometers and returns. During this short trip, the engine does not even heat up enough and suffers a lot, which affects its subsequent failure and thus maintenance costs. (Note: In terms of conversion, the diesel unit can consume more than 60 l / 100 km!).
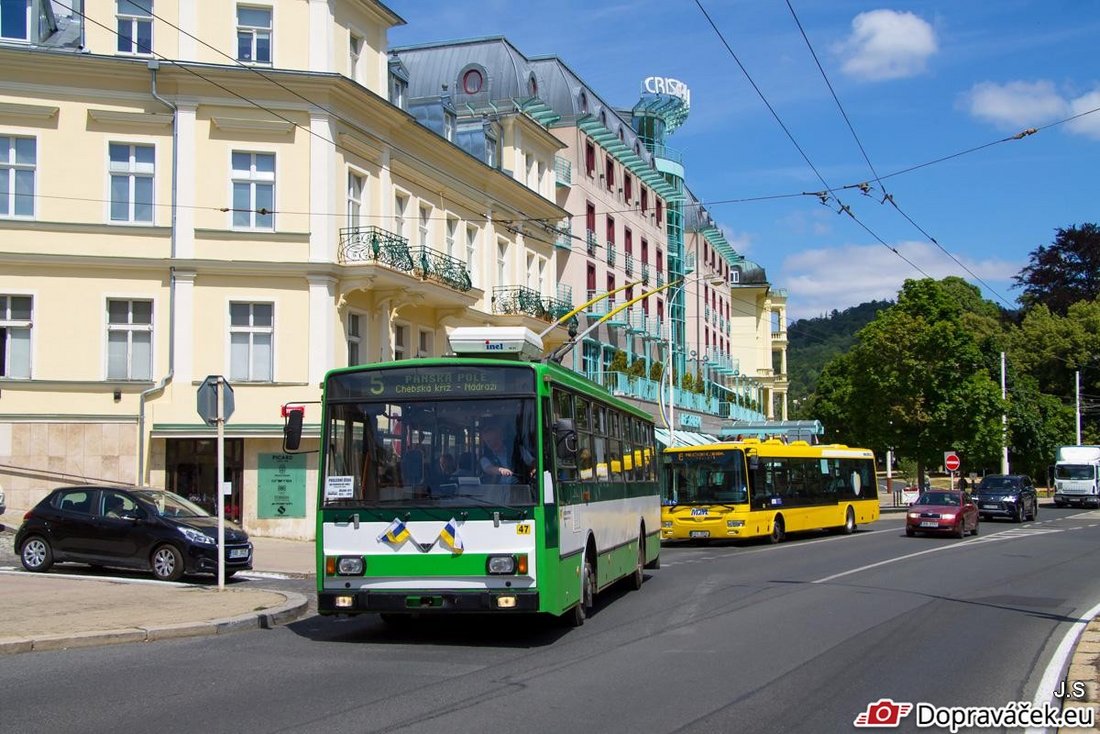
The battery drive in trolleybuses can serve as an auxiliary drive as well as a full-fledged drive. In the latter case, it is a challenge for traction batteries.
The use of a traction battery as a full-fledged drive means that the battery must drive electric motors with an output of 120 kW and more for 12-meter vehicles and over 200kW for 18-meter and longer vehicles in order to maintain the car’s dynamics. Partial trolleybuses are used many times a day for driving off the trolleybus line, and traction batteries are thus exposed to two challenging tasks:
The first task is to provide high performance and achieve many cycles during their planned lifespan. To this, we must add as a second task the requirements for the long lifespan of the traction battery – ideally the same as the trolleybus itself, before it is sent for overhaul.
Battery technologies for full operation outside the trolley
So let’s look at the individual battery technologies for full-fledged operation.
We will not intentionally deal with NiCd / NiMh technology (see the first part of our Battery University or nickel cadmium / nickel metal hydride batteries. These were used as traction batteries before the advent of lithium batteries and proved to be not entirely suitable, due to their size, maintenance requirements and other properties. We also drain lead batteries because they are too heavy.
Of the technologies currently used, we are left with lithium batteries, which in the vast majority of cases are used in today’s electromobility. Even among lithium batteries, there are several essential types. Let’s now look at the most used ones, which we can consider as suitable candidates for a traction battery for a partial trolleybus. For comparison, we will use several specifications that we will now introduce:
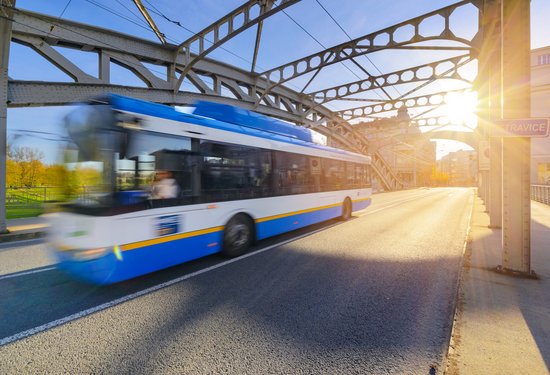
Table 1: Overview of lithium battery parameters
Parameter | Unit | Description |
---|---|---|
Specific energy | Wh/kg | How many Wh contains one kilogram of traction battery, ie the amount of energy in one kilogram of traction battery (imagine simply as the weight of the tank) |
Specific power | W/kg | Battery power per kilogram of its weight |
Energy density | Wh/l | The amount of energy that we place in the volume of one liter (imagine simply as the size of the tank) |
Power density | W/l | Power that can give us the volume of one liter of battery |
Number of cycles | Number of cycles | Number of charging and discharging cycles (we assume that for each battery we discharge and charge 80% of its total energy) |
C-Rate | Number of C | Continuous power / capacity ratio value |
Price per KWh | Kč/kWh | How many Kč does each kWh of battery cost |
Price per KWh cycle | Kč/kWh/number of cycles | Conversion to the price of one charge / discharge cycle |
Conversion to kilometer | Kč/km | Conversion to one kilometer driven at a consumption of 2 kWh / km |
Now imagine the candidates for the position of traction battery of a partial trolleybus. Electromobility in public transport is dominated by three lithium battery technologies: NMC (lithium nickel magnesium cobalt oxide), LFP (lithium iron phosphate) and LTO (lithium titanate oxide). These differ in their properties and price, and each of them is suitable for a different use.
Of all three technologies, NMC has the highest specific energy and energy density. Therefore, if we consider the same volume for the battery, the NMC will have the most energy measured in Wh in this volume. The same is true for mass – if we consider the same mass for all three technologies, NMC will have the greatest energy in Wh.
If we look at battery power, then the best technology is LTO, which provides the highest performance for the same volume and weight. LTO also leads in the number of charge-discharge cycles.
From a safety point of view, LTO is closely followed by LFP (lithium iron-phosphate) batteries.
A comparison of the parameters of our lithium battery technologies is in Table 2. To make the comparison fair, it is calculated from the battery system including the box without including the cooling unit.
Table 2: Comparison of traction battery parameters - Comparison from internal nano power data
Parameters | Unit | NMC | LFP | LTO |
---|---|---|---|---|
Specific energy | Wh/kg | 154 | 82 | 40 -50 |
Specific power | W/kg | 231 charging 171 discharging | 164 | 343 |
Energy density | Wh/l | 196 | 153 | 60 |
Power density | W/l | 269 charging 200 discharging | 306 | 462 |
Number of cycles | Number of cycles | 3.000 | 4.000 | 25.000 - 39.000 |
C-Rate | Number of C | 1C constantly | 2C constantly | 8C constantly |
Price per KWh | Kč/kWh | 14 000 Kč | 13 000 Kč | 40 000 Kč – 54 000 Kč |
Price per KWh cycle | Kč/kWh/number of cycles | 4,6 Kč | 3,25 Kč | 1,25 Kč – 1,52 Kč |
Conversion to kilometer | Kč/km | 9,2 Kč | 6,5 Kč | 2,5 Kč – 3 Kč |
Example
To simplify this complex comparison, let’s set a model example of traction battery requirements for full-fledged operation of a partial trolleybus.
Imagine a 12-meter trolleybus that has to travel 10 km 10 times a day on a traction battery with a consumption of 2 kWh / km. For each battery, we will count on the fact that at the beginning we can discharge a maximum of 80% of its energy, so we can count on the cycles according to Table 2. The required battery lifespan is at least 7 years, with each year the vehicle will be in operation 360 days each year. The vehicle requires 120 kW for propulsion.
From this word problem we calculate the basic indicators that we will use to select the traction battery and its correct size.
a) Service lifespan = number of cycles = 7 years × 360 days × 10 cycles / day = 25,200 cycles
b) Minimum energy required = 10 km × 2 kWh / km / 80% = 25 kWh
We need to choose a battery with a capacity of at least 25 kWh, which can deliver 120 kW and its lifespan is 25,200 charging cycles.
a) NMC a LFP battery
For NMC and LFP, we have to start from their performance limitations. The NMC has a current load factor (C-rate) of 1C and an LFP of 2C. (Note: C-rate, ie the coefficient of current carrying capacity, indicates the speed of charging and discharging the battery. For practical use, it represents the ratio of charging and discharging power of the battery in kW and its capacity in kWh). Traction batteries are therefore able to permanently provide power 1 × (at NMC) resp. 2 × (for LFP) as high as kWh of energy they contain.
The NMC battery therefore needs a capacity of 120 kWh and the LFP a capacity of 60 kWh.
With this capacity, the NMC battery will have a lifespan of 7+ years (the NMC battery will reach 25% of its energy when discharged to a total capacity of 25 to 30,000 cycles, which is sufficient for a requirement of 7 years).
However, the lifespan of the LFP battery will be less than 3 years, so we would have to replace the LFP 3 times for the required lifespan of 7 years.
b) LTO batteries
LTO has a C-rate of 8. Theoretically, a capacity of 15 kWh would be enough to cover 10 km, but we need 25 kWh. Battery power will be more than enough – 200 kW for charging and discharging. LTO technology reaches up to 39,000 cycles using 80% of the original energy, so the battery lifespan in this case will be more than 10 years.
If we calculate the acquisition costs of individual variants according to Table 2, the most expensive are LPF, which we have to replace 3 times with a total cost of CZK 2,340,000 and a lifespan of 8.3 years (3 times replacement). The NMC variant costs CZK 1,680,000 without the need for replacement and has a lifespan of 7 years. The LTO variant with a lifespan of 10 years works best for acquisition costs of CZK 1,350,000.
The above example serves as an illustration of the selection of the most suitable traction battery technology as an aid in the selection of traction battery requirements in partial trolleybuses. For the actual assignment, it is more appropriate to count on a higher than the minimum required capacity. In our case, where we need 20 kWh for 10 km, the optimal capacity of the LTO traction battery should be 40 kWh. Of this, 20 kWh will be for normal operation and the rest as a reserve for emergencies, which will also significantly extend the lifespan of the battery system. Our selected LTO system will use a lifespan of 100,000 cycles using 50% of the installed energy (equivalent to 10 km × 2 kWh / km from a 40 kWh battery). This would correspond to a traction battery lifespan of over 25 years.
Conclusion
For a partial trolleybus, which requires the full power of a battery drive, the most suitable chemistry for a traction battery is LTO chemistry or Lithium titanate oxide. This is due to the fact that the partial trolleybus needs a relatively short range on the traction battery, on the contrary, it places high demands on the number of charging cycles and the usable power of the traction battery. For this reason, even the technology with the highest price per kWh is the cheapest solution, because a partial trolleybus ideally uses a large number of LTO cycles. As we will say in other parts of the Battery University, choosing the right battery technology for specific applications is crucial. On the contrary, the advantages of one technology may be a disadvantage in other types of use, and therefore the current and future user should always pay due attention to the question of the choice of traction battery or stationary battery technology.