Design of traction batteries for heavy and industrial vehicles
How to choose a traction battery for our upcoming hybrid or electric vehicle? Which technology will be most suitable? How to know the flood of technologies and suppliers?
The design of an electric or hybrid vehicle can be said to begin and end with the battery. The type of traction battery determines the rhythm of the vehicle’s operation, primarily because of its charging rate and durability.
Recently, for traction have been used mainly lithium batteries. For some applications we can still see lead and nickel based batteries. But this is more of a historical drift for applications that have not yet been updated and don’t mind the high weight there.
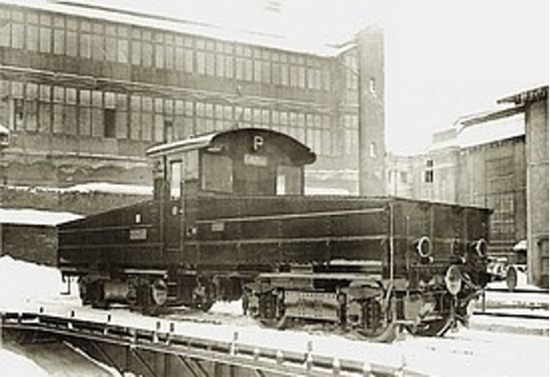
History
Lead-acid and Ni-Cd batteries started to be developed in the 19th century and therefore the first experiments with battery-powered vehicles were carried out with them. In commercial operation, they were used, for example, for trucks or shunting locomotives. In 1926, the battery shunting locomotive E 407.0 was produced by František Křižík and ČKD (electrical part – electrical equipment) and Breitfeld & Daněk (mechanical part – chassis). At the time of its production it was the largest battery locomotive in the world. 440 V with a capacity of 392 Ah (172 kWh) when discharged for one hour, and a capacity of 630 Ah (277 kWh) when discharged for five hours) [1].
Lithium batteries started to be developed in the 1980s and now we can say that we are at the time of their biggest boom to date.
Common electrical and hybrid applications of today
-
Industrial trucks used in warehouses and manufacturing plants (AGV, AMR)
-
Heavy-duty vehicles
-
Urban public transport (buses, trolleybuses, trams)
-
Rail transport (trains, locomotives, station shunters)
-
Port container handling equipment (RTG, Straddle carrier, AGV)
-
Airport equipment (GSE, Taxibot, baggage handling)
-
Trucks and excavators
-
Technical service vehicles (garbage trucks, material handling vehicles, multi trucks)
-
Boats (ferries, tugs, yachts)
-
-
Mining vehicles (drills, excavators, haulers)
-
Hybrid military vehicles with silent running
-
Passenger cars
The most common types of lithium batteries fpr traction
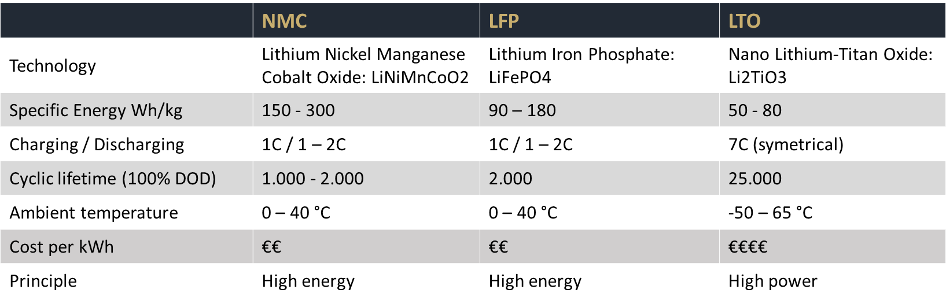
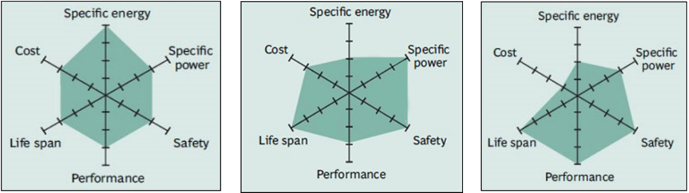
Main parameters for selecting battery technology
-
Required service life
-
Estimated number of cycles per day/year
-
Maximum load-bearing weight
-
Required power (charge/discharge) and voltage
-
Required range
-
Storage (inside the vehicle, on the roof of the vehicle)
-
Required IP (insulation)
-
Ambient operating temperature
-
TCO (total cost of ownership) or ROI (return on investment)
For the design and development of a battery system, it is essential that the battery system integrator approached has the experience or full support of the battery cell and module manufacturer.
The following tasks enter into the development of the system:
- Life cycle analysis based on power demand (load profile)Thermal analysis for cooling system design and storing the cells / modules in the box
- BMS design based on the number of cells in series and the number of parallel branches in the system
- Battery box design based on required standards and approvals (e.g. R10, R100, ISO 26262, SIL 0 – 3)
The main operating principles of today's electric and hybrid vehicles
-
Slow charging, Overnight charging, Depot charging (hours)
-
Long commutes
-
Suitable for NMC, LFP
-
-
Fast charging, Occasional charging, Charging during stops or downtime (on the order of 5 – 20 min)
-
24/7 operation possible
-
Suitable for LTO
-
-
Battery hybrid to cover power spikes and recuperate stored energy
-
Battery hybrid for silent and emission-free travel in the required area (5 – 20 km)
Examples of 24h operation
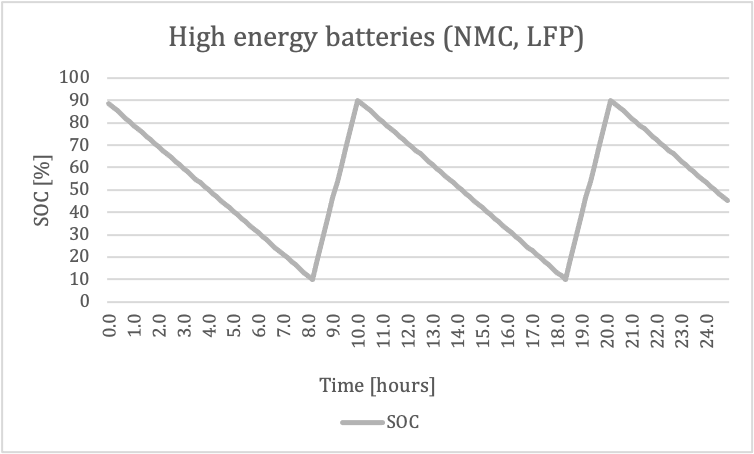
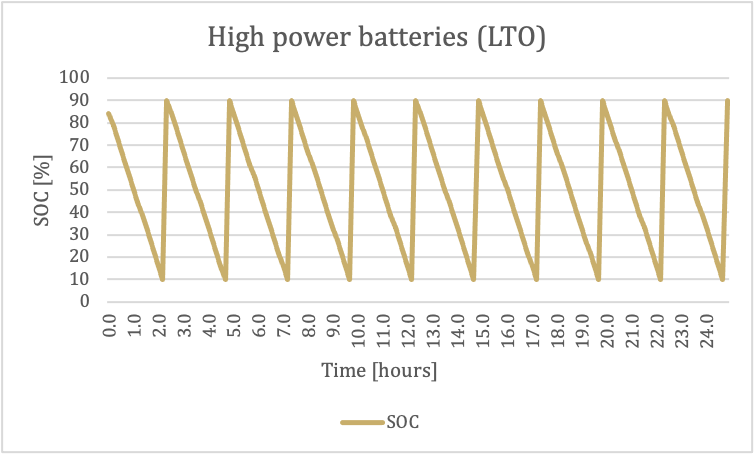
Conclusion
Traction battery system design can be done for any size vehicle. From small AMR robots (0.5 kWh), to buses and trains (50 – 600 kWh), to mining vehicles (MWh).
[1] https://www.koridory.cz/e-407-001-prvni-elektricka-lokomotiva-csd-uvedena-do-provozu-1926/
https://cs.wikipedia.org/wiki/Lokomotiva_E_407.0
[2] https://batteryuniversity.com/article/bu-205-types-of-lithium-ion