Traction batteries in heavy electric vehicles (4/5)
In addition to the partial trolleybuses and electric buses, which were similarly dealt with in the last two lessons of our Battery School, this time we will look at the use of batteries for other heavy electric vehicles in city traffic. These include, in particular, fuel cell and hybrid buses, battery trams and trains, heavy goods vehicles for urban services and other applications.
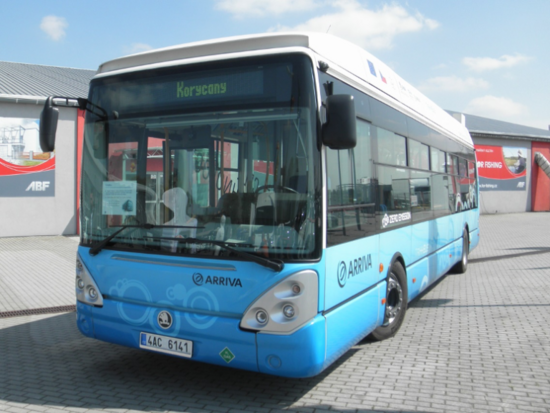
1. Fuel cell electric buses
a) Vehicles and their use
Hydrogen buses are sometimes also referred to in connection with fuel cell buses. However, this is not entirely accurate. Hydrogen can also be burned in a spark ignition engine, similar to, for example, natural gas. However, as test projects have shown, this use of hydrogen is also ecological, but very uneconomical. Therefore, hydrogen is now practically used without exception in a fuel cell, where the separation of an electron from a hydrogen atom, its subsequent conduction through an electrical circuit and its recombination with the remaining hydrogen cation and oxygen to water vapor creates a weak electric current.
The operational advantage of fuel cell buses over purely battery-powered drives is, above all, the range per tank filling comparable to a diesel bus – and it is precisely this advantage that drives fuel cell buses forward. The main disadvantage is the need for a hydrogen filling infrastructure as well as a more complex and expensive drive, reflected in the price of the vehicle.
In our battery school, we will not discuss this drive in detail, but we will take a closer look at the role of traction batteries in it.
b) Traction battery
There are two basic concepts of fuel cell bus propulsion.
In the first concept, the fuel cell is the main source of energy. An example of this concept is the Van Hool fuel cell bus. The main energy source is an 80kW fuel cell unit, which is complemented by 36kWh lithium-titanium oxide (LTO) batteries.
In the second concept, the main source of energy is the traction battery. It can be charged from a socket, similar to a “night” electric bus, and is charged while driving by a fuel cell with less power than in the previous case. Solaris, for example, uses this concept in its fuel cell bus.
Both concepts are correct and differ in their suitability for a particular type of operation. While a vehicle with a fuel cell unit with a capacity of 80 kW and more as the main energy source complete with a compensating small battery is suitable for urban and suburban traffic, a vehicle with a smaller fuel cell unit and a larger battery is also suitable for longer routes.
However, even this definition is not without exception. For some manufacturers, we find a lower power of fuel cells for this concept, eg 70 kW, and for some with a significantly higher, up to 120 kW. Let’s take a closer look at why.
The battery is always a necessary element in a fuel cell bus. Due to the physical nature of its operation (see above), a fuel cell can supply constant power, which, however, is not sufficient from the point of view of the demands of the bus drive system. Also, the system should not be turned off and on repeatedly. In short, fuel cells need to constantly supply energy with a constant output, such as 80 kW, as stated in the example of the manufacturer Van Hool. The energy from this hydrogen device goes to the traction battery, which through the traction converter supplies energy to the electric motors as well as energy to supply non-traction consumption. The required traction power for 12-meter vehicles is usually 200 to 250 kW, and therefore the traction battery must be capable of such a power load.
One of the key elements in city buses is weight, which is why a small battery is chosen for fuel cell applications, which serves as a balancing source. Its task is to match the required power for the drive and at the same time absorb the energy from recuperation during braking. The small battery has a small installation space and low weight, and these are key factors for a city bus. Cycles are also important, but less so than with fully electric buses. Such a city fuel cell bus stands quite often, and at these moments the traction battery is charged from the hydrogen system. The depth of discharge of the DOD battery is thus relatively small.
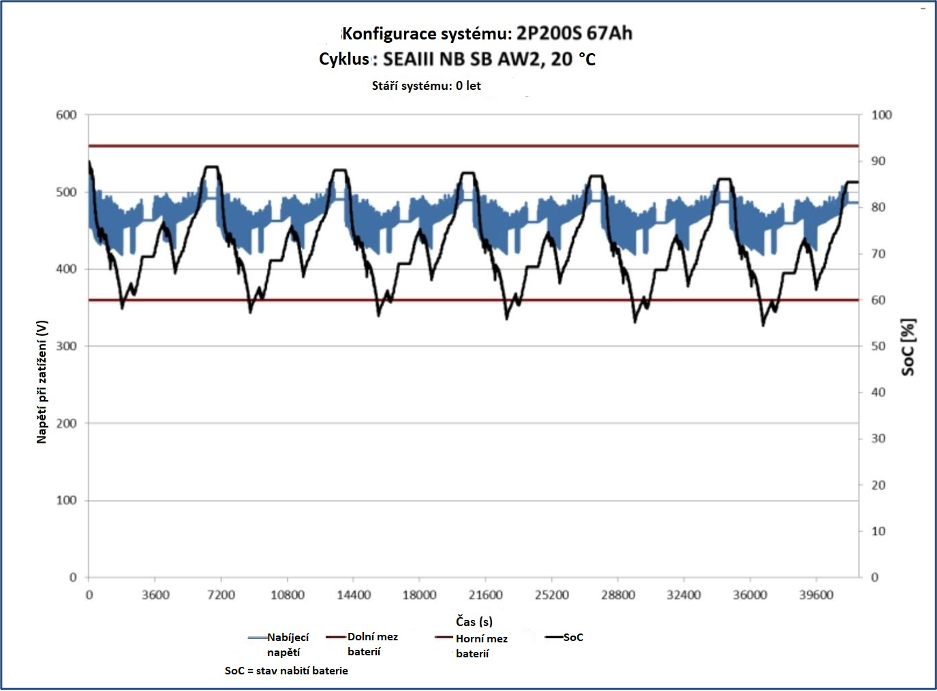
An example is graph 1, which shows a 40kWh LTO battery for a fuel cell bus in city traffic. As can be seen on the black curve, the energy used is in the range of 60–30%, ie at DOD = 30% (for the purposes of calculating the service life, we rounded the DOD value to 30%).
However, the challenge is temperature, because the performance of the traction battery is very high during operation and the battery thus produces a large amount of heat loss, which heats it. The cooling system must take care of this heat loss, but the operating temperature of the battery will always be higher than the temperature of the cooling medium, whether it is air or liquid.
In the example in Graph 1, the battery temperature rises to 45 ° C, and in Table 1 below we can substract the battery life.
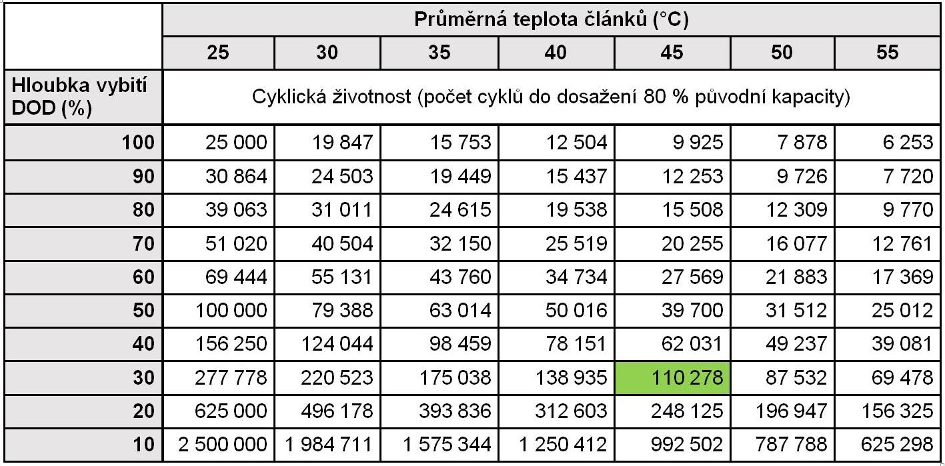
We know that the average battery temperature is 45 ° C and the depth of discharge of the battery at the beginning of its life is 30%. From the table, we simply subtract the number of cycles that the battery is capable of before its capacity drops to 80% of the original capacity. In the table, we have marked the cell that corresponds to this entry.
The graph shows that the battery is charged and discharged a total of 12 times a day, and if we consider that each such charge and discharge consume the same amount of energy, the battery will be capable of a total of 110 278/12 = 9 189 days of operation or up to 25 years.
Such a lifespan is unnecessarily long and there is room to optimize the battery, either to make more use of its capacity and reduce the performance of fuel cells, or to use a battery with a lower capacity. Lower capacity = lower price, lower weight, and these are two important areas.
While the first concept with the battery as the compensating element has the main energy source of the fuel cells, the second concept has the traction battery as the main energy source and the fuel cells serve for slower continuous charging. This concept is very similar to a classic electric bus, which has fuel cells as an effective tool to increase the energy in the system, and thus the range. On the contrary, the battery must be as large as possible in terms of capacity. However, in order to maintain sufficient occupancy of the vehicle, it must also have the lowest possible weight.
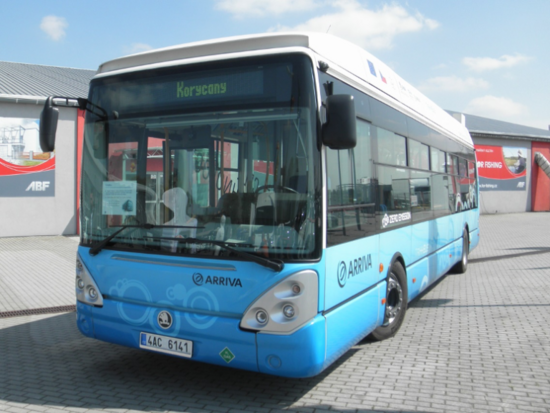
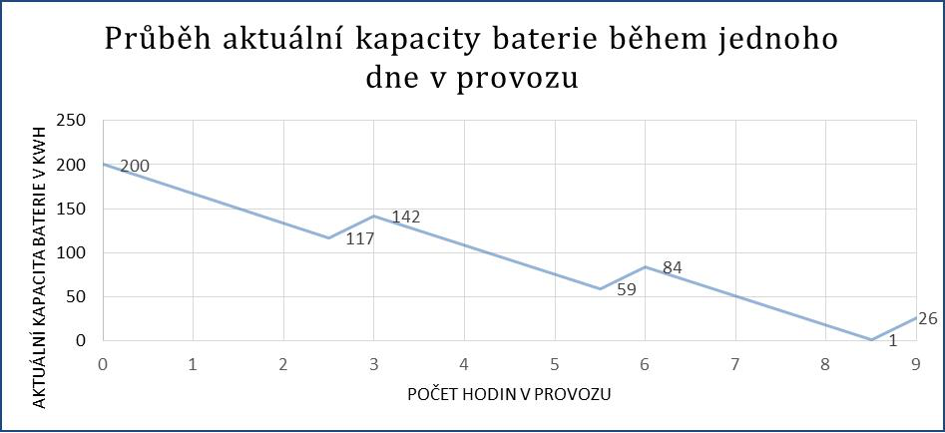
In Graph 2 we can see a simulation of a fuel cell bus with a large-capacity battery, here specifically 200 kWh, and with a fuel cell unit with an output of 50 kW. The bus always runs 100 km and then stops for 30 minutes. At the same time, the fuel cells still supply energy to the battery.
Since the battery will not be continuously charged by fast charging with high charging powers and its capacity is at the level of drive power (1C C-Rate => traction converter power = battery capacity), it is optimal to choose a lithium battery that has the highest specific energy, ie NCA (Lithium Nickel Cobalt Aluminum Oxide). However, it is usually unavailable due to the full utilization of manufacturers for passenger car electric transport, and therefore it is appropriate to use an NMC battery (Lithium Nickel Magnesium Cobalt Oxide). The cyclic load will be such that the battery will perform one full cycle during the operating day (say up to 80% of the depth of discharge), in which case the battery is able to run 3 to 4 thousand cycles according to the specific manufacturer. This corresponds to 4000 operating days or 11 years of operation 360 days a year.
However, it is also possible to consider an LFP (Lithium Iron Phosphate) battery, which, however, was practically not used in the fuel cell bus. LPF batteries have a significantly lower specific gravity compared to NMC (NMC for cells reaches a specific energy over 220Wh / kg, some LFP manufacturers state a specific energy value of up to 120 Wh / kg). If we theoretically use a 100kWh LFP battery that handles short-term 2C power, ie 200 kW and which we charge with 100 kW from fuel cells, we could use such a battery as a third concept halfway between the concept with a small LTO battery and a large NMC batteries.
Now let’s compare the weights of both NMC and LFP batteries (consider only battery cells). The NMC will have a capacity of 200 kWh and a specific energy of 220 Wh / kg. The LFP will have a capacity of 100 kWh and a specific energy of 120 Wh / kg). In this case, both batteries will be approximately the same. However, a 100kWh LFP battery will be significantly cheaper than a 200kWh NMC battery.
2. Hybrid Buses
a) Vehicles and their use
Today, diesel-hybrid buses are experiencing a certain renaissance, because batteries are used for electric propulsion at start-up (in the order of hundreds of meters, up to a speed of about 20 km / h) and are charged by recuperation during braking. The main drive remains diesel, but thanks to the hybrid set, up to 30% of fuel can be saved, not to mention starting noise. This drive is offered by most bus manufacturers today. Here, in addition to batteries, supercapacitors are also used as energy storage, which are more resistant to frequent charging and discharging, and their order of magnitude lower energy density is not a major complication here.
The plug-in hybrid drive combines a fully electric drive with plug-in charging and a diesel engine. For example, the 12m plug-in hybrid (or electric hybrid) Volvo bus has a fully electric range of about 7 km on a single battery charge. When the capacity drops or when additional power is required, the drive is switched to hybrid, where the torque is automatically distributed between the electric motor and the diesel engine according to the current operating conditions.
b) Traction battery
City traffic, whether it is a car or a hybrid city bus, is burdened by frequent stops and starts. This means high performance for both vehicle start-up and energy recovery back to the energy storage. We intentionally use the name energy storage because, as we mentioned in the introduction to hybrid buses, some use supercapacitors instead of batteries. These have the advantage of being able to deliver a very high C-Rate and have a long cycle life, making them ideal for a Start-Stop hybrid drive. For example, Mercedes with the Citaro Hybrid follows this path.
The concept of a hybrid bus with a battery is very similar – a small battery supplies energy for starting and recuperates the braking energy back. Hybrid vehicles use not only lithium ion batteries, but also other chemicals, such as NiMH (nickel metal hydride batteries). In the case of a hybrid drive, their energy stores, whether supercapacitors or batteries, are used with a very small depth of discharge and are therefore able to achieve a long service life, just like the vehicle itself.
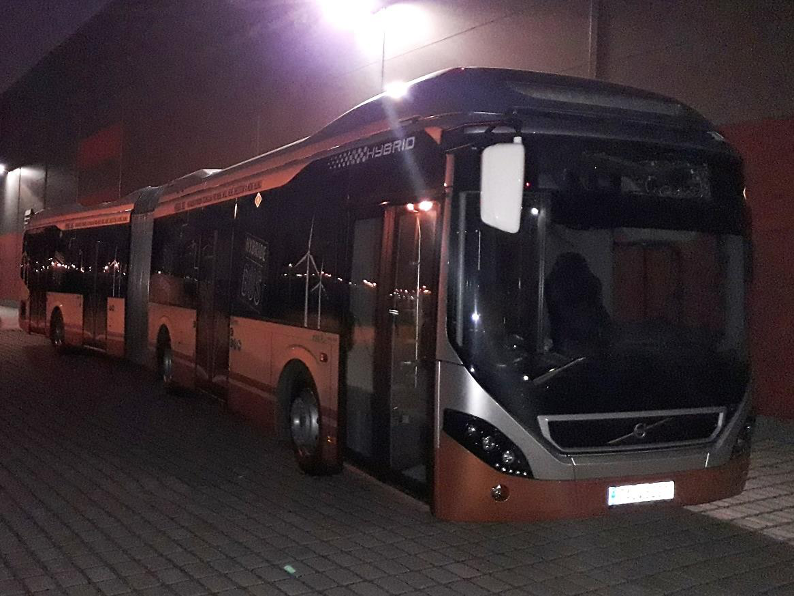
Unlike hybrid vehicles, the concept of plug-in hybrid vehicles is more similar to conventional electric buses. The battery can also be recharged with an external charger. The difference is that the range of pure batteries is significantly smaller compared to electric buses, usually up to 10 km. Therefore, if we count on consumption of 1.5 kWh / km, as in the previous lesson on electric buses, and set the condition of the end of battery life when reaching 80% of the original capacity, the hybrid battery should have a capacity of at least 18.75 kWh.
Let’s take a look at the whole powertrain. Plug in hybrids can have two types of drives. In the first type, the electric motor and the conventional combustion engine work in parallel (so-called parallel hybrid), ie they can work together or each separately, or share the required drive torque together. The second type of hybrid drive is one in which the internal combustion engine acts as a generator motor that charges the battery, which then supplies the electric motor / motors (so-called serial hybrid).
To illustrate the difference in traffic between PHEV and HEV (plug-in hybrid and hybrid), Figure 3 is shown below.
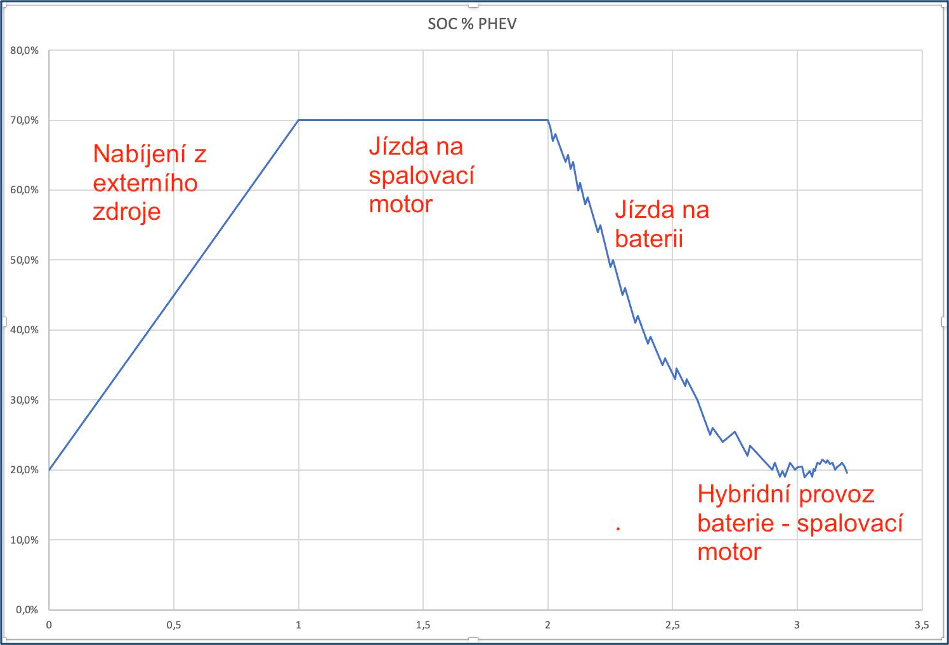
The difference between PHEV and HEV is how the battery is operated. PHEV can be operated as shown by the entire curve from start to finish – charging, driving on an internal combustion engine, driving on battery only and hybrid mode engine + electric motor. In HEV operation, the battery operates only as the last part of the displayed curve – it always oscillates along a certain limit of the SOC state of charge.
3. Rail vehicles with batteries for passenger transport
a) Vehicles and their use
Trams with battery tanks for operation without trolley are also used in urban transport abroad. It is usually a short section of hundreds of meters to several kilometers.
An example is the Škoda ForCity Classic tram for the Turkish city of Konya. The length of the track here is 4 km below the trolley and 2 km of the track without the trolley. The tram for this project is designed for independent travel up to 15 km.
On a larger scale of capacity and power, we encounter the use of traction batteries in passenger trains (electric units), in which the battery energy storage solves the problem of electrical operation on shorter non-electrified sections adjacent to the main electrified line without having to proceed with their investment-intensive electrification.
An example is the Stadler Flirt Akku electric unit for the German regional carrier NAH.SH. These electric units will have a battery range of up to 150 km under optimal conditions. The longest non-electrified section where they will be operated is expected to be 80 km long – similarly to the case of trams for Konya, there is therefore enough operational reserve. The batteries will be recharged from the contactor infrastructure when staying at five stations and while driving on the line.
b) Traction battery
The choice of a suitable battery application for rail vehicles depends, as with electric buses, and therefore all electric vehicles, on the operation for which they are intended. It can be said that the operation of battery-powered rail vehicles is still in its infancy, so to speak, and we can find a few projects around the world that are gaining experience with battery-powered vehicles. As can be seen from the introduction, rolling stock also needs to be divided into urban applications, such as metro and trams, and railway applications, which are passenger and freight trains.
For urban applications, a small distance in the order of several kilometers for battery operation is typical. Therefore, the capacity of the battery does not have to be large, but the battery must be capable of high discharge performance and have a long cycle life. The most suitable for urban rail vehicles is the lithium titanium oxide (LTO) battery, which with low capacity can provide sufficient power for the propulsion system and at the same time has a long cycle life, so the operator does not have to worry about having to change the battery often.
When designing the correct configuration of the battery, ie its capacity, it is optimal to simulate the operation on the battery, which will confirm whether it is correctly selected in terms of voltage, capacity and performance of the battery.
The analysis of battery operation is already shown in the section of fuel cell buses in graph 1. An example of the analysis of city tram battery operation is in graph 4. The analyzed battery has a configuration with a nominal voltage of 460 V DC and a capacity of 60 kWh.
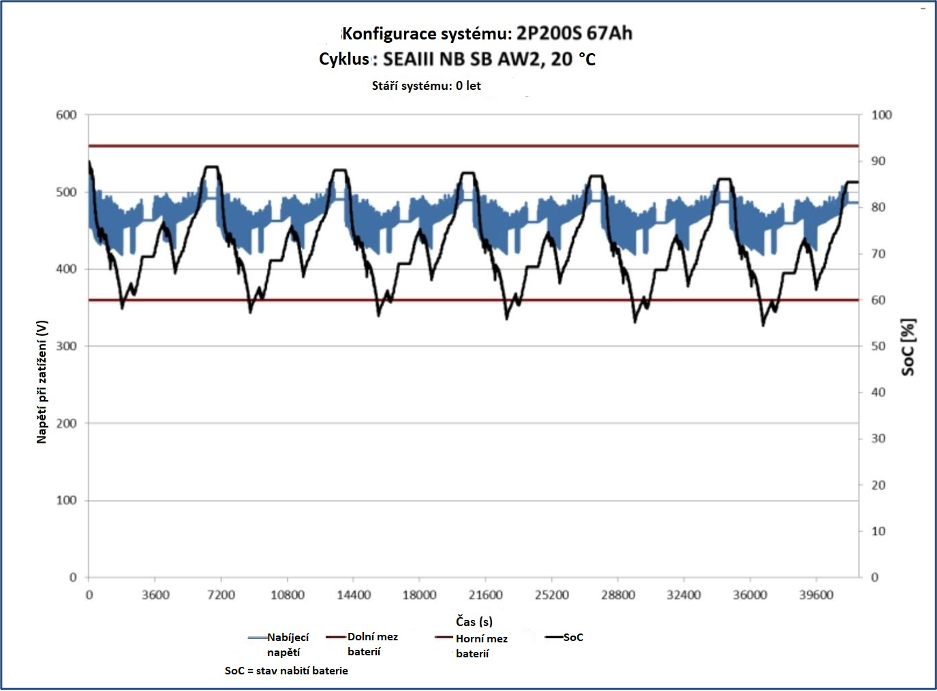
For train applications, the type, configuration and use of the traction battery vary greatly. However, it can be said that there is a lot of space on the tracks for the electrification of train transport, both freight and passenger. We have already mentioned the Stadler Flirt Akku kit using LTO batteries, as well as, for example, the Desiro ECO electric unit from Siemens. In general, LTO dominates rail applications.
But let’s look at other chemicals and examples of their use. NMC technology is used by Bombardier in Talent 3 trains. This technology is also used in Alstom Coradia iLint H2 trains, which have fuel cells as their main energy source, operating on the principle described above for fuel cell buses. Lithium iron phosphate batteries are used in Elektrostar trains manufactured by Bombardier.
The future on rails is not only in pure battery, but also in hybrid and fuel cell applications. Whichever of them dominates, one thing is clear. The world on tracks is following trends in transport, as well as passenger, bus and freight transport.
4. Heavy electric trucks for urban traffic
a) Vehicles and their use
Heavy electric trucks for urban services and urban freight transport are still in their infancy when it comes to commercializing traffic. Nevertheless, they can play an important role in improving conditions in the city, whether in terms of emissions or annoying noise – keep in mind that these vehicles often run on the fringes of the day when most people sleep.
Here it must be taken into account that the ratio between the energy consumption for the self-driving and for the auxiliary drives will be significantly different than, for example, for electric buses on the line. While the electric bus is mainly about electric heating and air conditioning, for example, in the case of a garbage truck, it is also necessary to drive the superstructure for loading, unloading and compressing waste. It is necessary to adapt their equipment with traction batteries and operating mode.
An example of such a vehicle platform is the Volvo FE Electric electric truck with a gross weight of 27 tons and batteries with a capacity of 200-300 kWh. It is expected that they will reach up to 200 km on a single charge, fast charging 150 kW DC from a standardized CCS socket for approx. 1.5 hours and slow charging 22 kW AC for approx. 10 hours.
b) Traction battery
The selection of a suitable battery for this type of vehicle is no longer only related to a specific project, as is the case, for example, with electric buses. For the electrification of vehicles for municipal services, more standard products from various manufacturers are offered.
As far as traction batteries are concerned, the operation of these vehicles is most similar to night-charging buses. The traction battery must have sufficient capacity for all-day operation of the vehicle, and in the case of garbage trucks, emphasis is also placed on the size of the traction battery.
5. Examples fpr other battery drives
This category mainly includes the use of battery electric drives, which were discussed earlier in our School, in a less usual way.
a) Example: electromobile public library
An example is the use of two electric buses as mobile city libraries in Gothenburg, Sweden. The basis of their construction is a standard 12m Volvo electric bus, the body of which was modified by a specialized Finnish manufacturer into an attractive library (see the article in the brochure Electric buses for the city IX ). The energy storage here is a 250 kWh traction battery, charged overnight with a standardized CCS / Combo2 socket. The mobile library will cover approximately 70 – 80 km throughout the day. From the point of view of driving itself, the traction batteries would be quite oversized. However, it is necessary to take into account the necessary non-traction consumption for heating and air conditioning, which is much higher here per kilometer than for line traffic.
For similar non-traditional applications, it is possible to consider the use of batteries from line vehicles, which have already been replaced by others. Even if the capacity of these used batteries is already 80% or less of the original value, they can still be a full-fledged source of energy for a vehicle that does not drive as often as a regular car and that does not strictly address occupancy. For example, if the design of the vehicle allows for a given specific use, more batteries from the original vehicles can be used here. This would significantly extend the life of the batteries not only in stationary applications, which we will talk about in the next lesson of our Battery School, but also offer their operation in the mode for which they were originally designed and manufactured – the vehicle.
b) Example: Electric boats
If we extend urban transport to shipping, we get, for example, the operation of electric boats on the Brno dam . The source of energy for their drive are 300V lead traction batteries with a capacity of 336 kWh, respectively. 1120 Ah; the control voltage is 24 V. Lead-acid batteries perform a dual function on the ship: in addition to the electrical energy storage, they also serve as ballast at the bottom of the ship, which gives it the necessary stability. The large weight of lead-acid batteries, which is a problem everywhere else, thus becomes an advantage in the case of electric ships.
As with wheeled vehicles, there is no one-size-fits-all technology that saves all types of shipping at once, but it is necessary to carefully determine the requirements for battery operation – distance per charge, requirements for charging frequency, charging and discharging power, etc. applications, we most often encounter either a lead-acid battery or an LFP battery in smaller vessels. But there is also an application with an LTO battery, such as the test electric boat AiriEl for 80 passengers from the manufacturer BB Green.
.
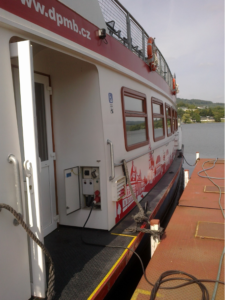
In short, green is the tree of life, not excluding battery drives.
František Šťastný, EBZ nano power sr.r.o.
Jakub Slavík, Smartcityvpraxi.cz
Photo © Smartcityvpraxi.cz